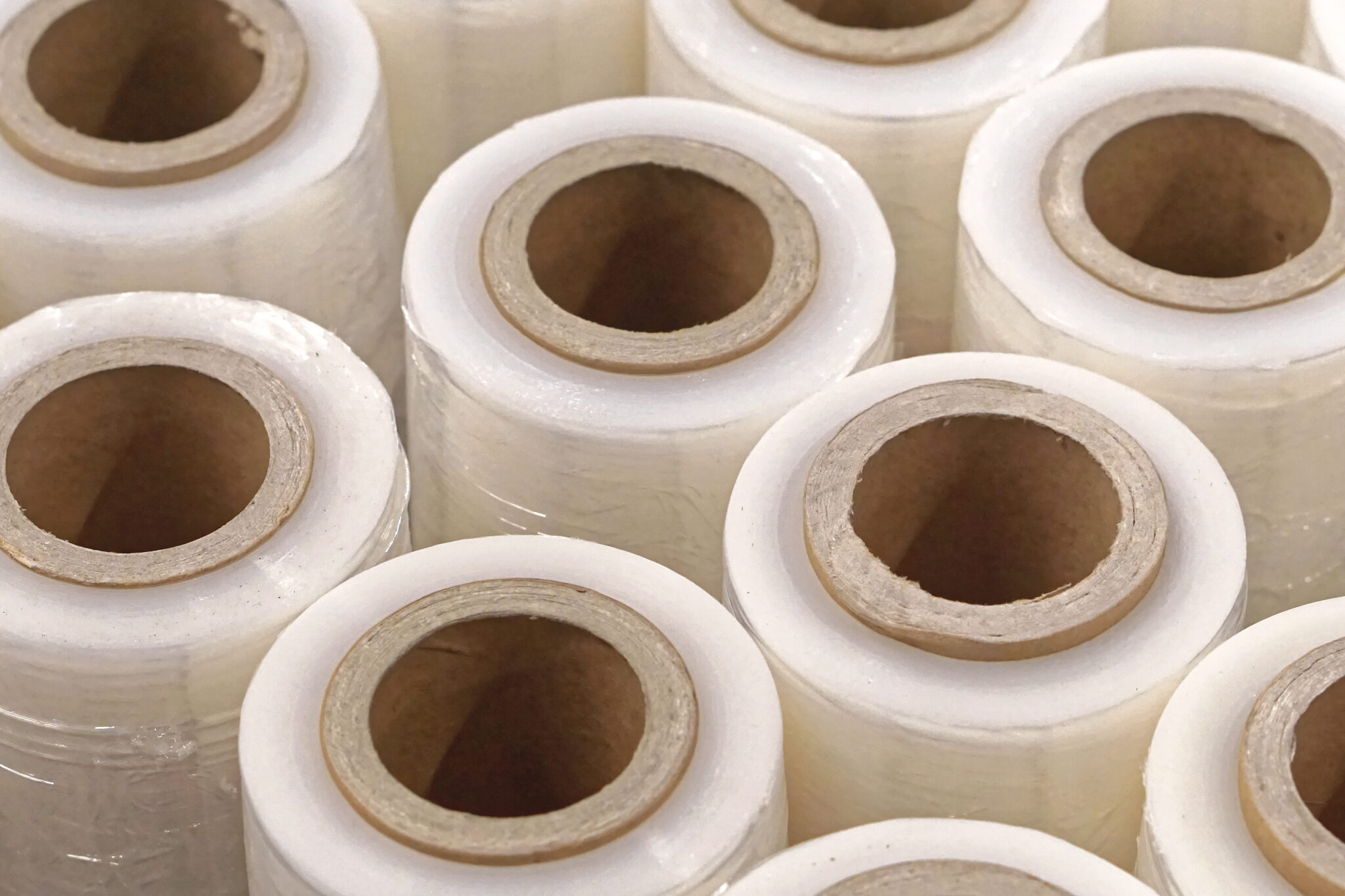
Film Alternatives Project
Evaluating Performance and Environmental Impacts of Stretch Film Alternatives
A Deeper Understanding Of Load Wrapping Solutions For Sustainability
This project included an investigation into current stretch wrap alternatives. The evaluation compares performance, weight, cost, and estimated environmental impact across representative samples. Lantech utilized industry leading test equipment and technology to achieve containment force with drastically different material properties. Lantech filed several patents related to testing outcomes and evaluated new samples in late 2023.
To learn more download the white paper (revised February 17, 2025) or contact us to discuss further.
Key Takeaways
Frequently Asked Questions
Post-consumer recycled (PCR) stretch film is collected after it has been removed from loads at the ultimate destination. It then must be sorted, and cleaned of labels, adhesive, ink, and foreign matter before being pelletized into resin for blending with virgin resin to produce PCR stretch film. It is distinguished from Post Industrial Recycled (PIR) stretch film made from scrap or returned goods collected by the film producer.
The gels, and non-compatible materials in PCR dramatically impact the ability to pre-stretch the film without excessive film breaks. Reducing pre-stretch to avoid film breaks generally doubles the film weight to achieve the required containment force. Lantech views film breaks as the key risk of PCR.
Optimizing normally requires experimenting with materials, and all machine settings to find the pre-stretch, tension, that provides the required containment force at the lowest film weight without film breaks. This is sometimes a tedious and time-consuming process that may have to be repeated if the film quality, load profiles, or machine performance varies. When comparing wrapping materials, it is critical to compare their performance only after each has been optimized. Using Lantech Film Auditor, 1000’ film samples were run at the equivalent of 35 RPM at progressively lower pre-stretch until no holes were observed. The result of this test prescribed a pre-stretch level.
While the ultra-PCR sample demonstrated significantly improved results, it was a single sample. The critical part of demonstrating high performance for PCR is a replication of success for thousands of loads in real-world environments. The variation in performance can make or break sustainable outcomes as operators will need to reduce film breaks and change machine settings to withstand inconsistencies in the film. If machine settings are reduced or degraded, more film than the optimized amount will be applied to the load; therefore producing different results than what we show in the optimized results data set.
Overall, it is a challenge to get valid carbon footprint information on all variants of PCR. Although, the LCA of a material is an accepted source for carbon footprint and its relative environmental impact. We have adopted the CO2 impacts of all materials from Mondi’s well-researched “Advantage Life Cycle Assessment” (2021) assuming the recycled end-of-life scenario. We multiplied the gram weights of our results by the carbon footprint factor from Mondi, for a gram-weight-adjusted carbon footprint estimate. Each specific blend of PCR or virgin film may vary, so our category estimates are used for illustrative purposes only. Mondi reserves the right to modify carbon footprint data for its products and publications.
Please fill out the information below and hit SEND MESSAGE.
"*" indicates required fields